Demir Ve Çelik
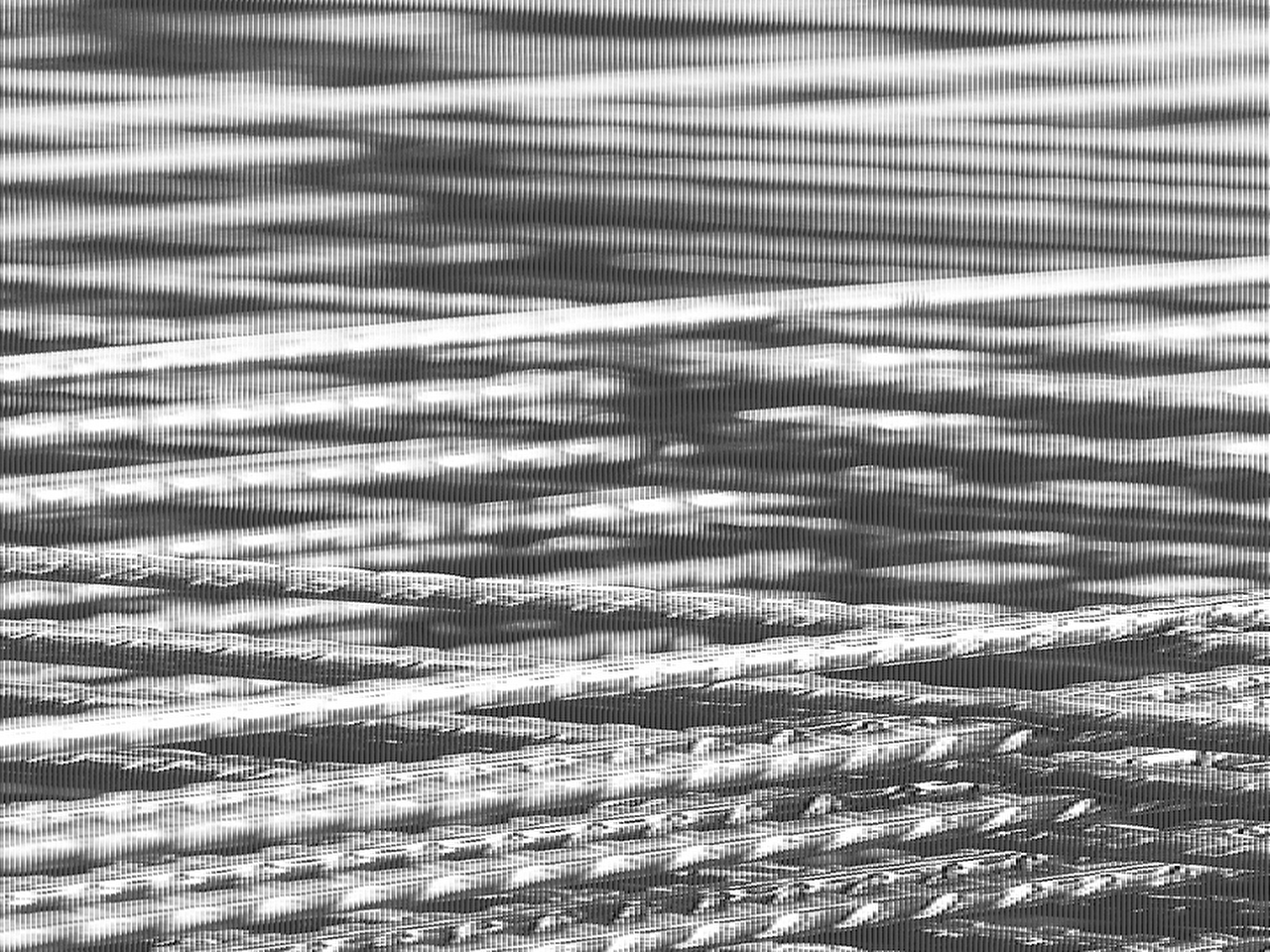
Demir yeryüzünde en bol bulunan ve en çok kullanılan metallerden biridir. Demirden elde edilen çelik ise sağlamlığı, yüksek çekme ve kopma direnciyle demirden çok daha geniş bir kullanım olanağı sunar. Gemilerin, demiryollarının ve otomobillerin temel yapım gereci çeliktir. Çekme ve germe kuvvetlerine karşı son derece dayanıklı olan çelik bulunmasaydı yüksek gökdelenler ve uzun köprüler yapılamazdı. Üstelik bütün magnetik maddeler arasında demir ve çelikten daha bol bulunanı ya da daha ucuza üretileni olmadığından, bu gereçler bilinmeseydi elektrik üretimi böylesine yaygınlaşamazdı. Bütün elektrik üreteçlerinin yapım ilkesi demirin mıknatıslanma özelliğine dayanır; ayrıca elektrik üretiminde büyük önem taşıyan buhar türbinleri de yüksek sıcaklıklara dayanıklı çelikten yapılır. Bunların dışında, bugün kullandığımız alet ve gereçleri üreten makinelerin hemen hepsi demir ve çelikten yapılmadır.
Yerkabuğunun yaklaşık yüzde beşini oluşturan ve yerçekirdeğinin temel bileşeni olan demir yeryüzünde en bol bulunan elementler arasında ilk sıraları alır. Bütün canlıların yapısında demir vardır; kandaki hemoglobinin ve yeşil bitkilerdeki klorofilin bileşenlerinden biri olarak canlıların yaşam süreçlerinde önemli bir rol oynar.
Kimyasal simgesi Fe, atom numarası 26, atom ağırlığı 55,847 olan demir element halindeyken gümüş beyazlığında, oldukça yumuşak ve magnetik bir metaldir. Ama doğada element halindeki serbest demire çok ender rastlanır; genellikle meteoritlerin (yeryüzüne düşen büyük göktaşlarının) bileşiminde bulunan bu serbest demir de çoğu kez yüzde 5 ile 7 oranında nikelle karışmıştır. Bunun dışında demir yerkabuğunda hep bileşikler halinde bulunur. Nemli havada kolayca oksitlendiği için de en yaygın bileşiği demir oksitlerdir. Demir cevherlerindeki bu kırmızı ya da siyah, sert ve ağır minerallerden demiri ayırarak katışıksız metal halinde elde etmenin yolu bulunduğunda insanlık tarihi Demir Çağı’na girmiştir.
Bir demir cevheri yaklaşık yüzde 20’nin üstünde demir içerdiği zaman işlenmeye değer görülür. Dünyanın en zengin demir yatakları ABD ile Kanada sınırı üzerindeki Superior Gölü çevresinde, Fransa-Almanya sınırı yakınlarında ve SSCB’dedir. Ayrıca Avustralya, Brezilya, Venezuela, Güney Afrika, Hindistan, İspanya, Gabon, İsveç ve Cezayir’de verimli olarak işletilen zengin demir yatakları vardır. Türkiye’nin en önemli demir yatakları ise Divriği çevresindedir.
Demir cevherinde kum, kil ve su gibi katışkıların yanı sıra, özellikle çeliğin niteliğini bozduğu için giderilmesi gereken fosfor ve kükürt gibi elementler de bulunur.
Cevherden Demir Elde Edilmesi
Element halindeki demiri ayırmak için demir cevherinin bir yüksek fırında eritilmesi gerekir. Yüksek fırın çelikten yapılmış ve içi ateşe dayanıklı tuğlalarla astarlanmış, dik duran çok büyük bir silindir biçimindedir. Günümüzde kullanılan yüksek fırınların çapı 9 metreyi, yüksekliği ise 24 metreyi bulur. Bu eritme fırını iyice karıştırılmış demir cevheri, kokkömürü ve kireçtaşıyla sürekli olarak beslenir. Eğer demir cevheri ince taneliyse önce kömürle ısıtılır ve “klinker” ya da “sinter” denen yumrular haline getirildikten sonra yüksek fırına yüklenir. Fırının dibine yakın bir yerden giren ve çok sayıda memesi ya da hava deliği olan bir borudan içeriye sürekli sıcak hava gönderilir. Sıcak hava fınnın içindeki karışımın arasından yukarıya doğru çıkarken kokkömürünü tutuşturur. Bu yanma sırasında kömürdeki karbon demir oksidin oksijeniyle birleşerek karbon monoksit oluştururken, serbest kalan demir eriyerek aşağıya doğru akar ve fırının dibinde bir havuz oluşturur. Bu arada kireçtaşı da cevherin içindeki kum, kil gibi katışkıları eriterek sıvı bir karışıma dönüştürür. “Cüruf” denen bu artık madde karışımı fırının dibine doğru akarak erimiş demir havuzunun üzerinde bir katman halinde yüzer. Kireçtaşı ayrıca kükürt ve fosforla da tepkimeye girerek bu istenmeyen elementleri büyük ölçüde demirden ayırır.
Dipte oluşan ve yukarıya doğru yükselerek fırının tepesinden açığa çıkan yüksek fırın gazları da değerli bir yan üründür. Karbon monoksit içeren bu sıcak gazlar yüksek fırının içine püskürtülen havayı ısıtmak, ayrıca buhar ve elektrik üretm ek için kullanılabilir.
Fırının dibinde biriken erimiş demir yaklaşık her beş saatte bir potalara ya da taşıma kaplarına akıtılır. Henüz sıvı haldeyken buradan ya çelik üretim birimlerine gönderilir ya da dökme demir elde etmek üzere kalıplara dökülür. Erimiş demirin üzerinde yüzen cüruf da yaklaşık her iki saatte bir başka bir delikten akıtılarak fırının dışına alınır. Yüksek fırın cürufu birçok alanda kullanılan değerli bir yan üründür. Karayollarının üzerine döşemek ya da demiryollarında traverslerin altını beslemek için kullanılan küçük kırma taş (balast) üretiminde, buharla köpürtülerek tuğla yapımında ve ince tane halinde öğütülerek çimento yapımında bu cüruftan yararlanılır.
Yüksek fırında üretim süreklidir; fırın bir kez ateşlendikten sonra altı yıl ya da daha uzun bir süre hiç söndürülmeden çalıştırılır. Bu süre dolunca fırının bakıma alınarak içindeki ateşe dayanıklı astarın yenilenmesi gerekir; çünkü tuğlalar fırına yüklenen karışımın aşağı doğru hareketiyle aşınmıştır.
Yüksek fırın teknolojisi hızlı bir gelişme içindedir. 1930’da böyle bir tesisin günlük üretimi en çok 1.000 ton dolayında iken 1960’ta bu kapasite 3.000 tona, 1970’te 7.000 tona ulaştı. 1980’lerde ise her birinin günlük üretimi 10 bin tonu bulan birkaç yüksek fırınla donatılmış dev tesisler kuruluyor. Bu üretim düzeyine ulaşabilmek için fırının büyük bir hızla ve olağanüstü miktarda hammaddeyle beslenmesi gerekir. Günümüzde fırına püskürtülen hava oksijenle, buharla ya da fueloil, toz kömür gibi sıvı ve katı yakıtlarla zenginleştirilir. Çoğu kez maden ocağındaki cevherin zenginleştirilmesi de verimi artıran etkenlerden biridir.
Dökme Demir ve Dövme Demir
Yüksek fırında üretilen erimiş demirin büyük bölümü çelik, geri kalanı da dökme demir yapımında kullanılır. Sıvı haldeki demirin kalıba dökülerek katılaşmasıyla elde edilen dökme demir özel kalıp makinelerinde üretilir. Bu makinelerde bir sonsuz zincir üzerinde sürekli dönen çok sayıda metal kalıp vardır. Erimiş demirle doldurulan her kalıp zincirin üzerinde ilerlerken soğuk su püskürtülerek soğutulur. Yolun sonunda zincir aşağıya doğru kıvrılırken bu kalıplar da ters döner ve içindeki katı demir külçesi aşağıda bekleyen bir vagonun içine düşer. Dönen zincir boş kalıbı taşıyarak ilk konumuna getirir; kalıbın içine kireçli su püskürtüldükten sonra yeniden erimiş metal doldurulur ve işlem böylece sürer. Külçe halindeki bu dökme demir piyasada daha çok “pik” ya da “font” adıyla bilinir. İlk terim “ham külçe” anlamındaki İngilizce pig sözcüğünden, İkincisi ise “dökme” ya da “dökülmüş” anlamındaki Fransızca fonte sözcüğünden dilimize geçmiştir. Ham külçe denmesinin nedeni de bu kalıp halindeki demirin yeniden eritilerek bir ölçüde arıtıldıktan sonra kullanılabilecek bir hammadde olmasıdır. Gerçekten de dökme demir külçeleri üretilecek eşyanın ya da parçanın biçimindeki döküm kalıplarına akıtılmadan önce yeniden eritilir. Demir döküm atölyelerinde pik demiri eritmek için kullanılan “kupol ocakları”nın, üstten yüklenen karışımın ham demir külçesi ve kokkömürü olması dışında yüksek fırından bir farkı yoktur. Demir külçesi bu fırında yeniden sıvı hale geçerken içindeki katışkıların bir bölümünden temizlenir. Ama gene de oldukça yüksek oranda karbon ve silisyum içeren bu alaşım, dövme demir gibi çekiçle dövülemeyecek kadar gevrek ve kırılgandır. Bu yüzden ancak kum kalıba döküm tekniğiyle biçimlendirilebilir. Kalorifer kazanları ve kömür sobaları, motorlu araçların silindir blokları ve fren kampanaları (tamburları), çeliği külçe (ingot) halinde dökmek için kullanılan külçe kalıpları, hadde tezgâhlarının merdaneleri, tarım aletleri, çeşitli makine parçaları ve ocak ızgaraları daha çok dökme demirden yapılır.
Oysa genellikle yüzde 0.1'den daha az karbon içeren dövme demir hemen hemen katışıksız ve çekiçle ya da presle dövülerek biçimlendirilebilecek kadar sünektir. Özellikle akor dereceye kadar ısıtılıp hamur ya da macun kıvamına gelecek kadar yumuşadığında kolayca dövülebilir, kaynaklanabilir, takım tezgâhlarında işlenebilir. Ayrıca açık havada oksitlenmeyen, basınca ya da yük taşımaya ve darbelere çok dayanıklı olan dövme demir yerini çeliğe bırakıncaya kadar sanayinin en önemli gereçlerinden biri olmuştur. Eskiden hemen hemen bütün aletler kor halindeki sıcak demirin örs üzerinde çekiçle dövülmesiyle üretilirdi. Bu sıcak demircilik yerini giderek soğuk demirciliğe bıraktı ve demiri eskisi gibi elle değil çeşitli alet ve makinelerle işleyen demirci ustaları haddelenmiş hazır sanayi demirinden kapı ve pencere pervazları, balkon demirleri, korniş, direk gibi “demir doğrama” ürünleri yapmaya başladılar. Günümüzde yapı doğramalarında daha çok alüminyum ve çelik kullanıldığından soğuk demircilik de geleneksel küçük sanayi dalları arasına katılmıştır.
Çelik ve Çelik Üretimi
Çelik yüzde 0,05 ile yüzde 1,5 arasında karbon içeren bir demir-karbon alaşımıdır. Çeliğin ne ölçüde sertleştirilebileceği de bu karbon oranına bağlıdır. Karbon oranı ne kadar yüksekse, özel ısıl işlemlerden geçirilen çelik de o kadar sert ve aşınmaya dirençli olur.
Toplam çelik üretimi içinde en büyük payı, sanayide yaygın ama yanlış bir adlandırmayla karbon çeliği olarak bilinen adi ya da standart çelikler alır. Basit bir demir ve karbon karışımı olan bu çeliklere manganez, nikel, krom, silisyum ve molibden gibi başka elementlerin katılmasıyla da .özel alaşım çelikleri elde edilir. Sertlik ve dayanıklılık, özellikle çekme ve germe kuvvetlerine, darbelere, sürtünmeyle aşınmaya, paslanmaya, sıcaklığa ve kimyasal maddelerin aşındırıcı etkilerine (korozyona) karşı direnç alaşım çeliklerinin özel niteliklerinden bazılarıdır. Paslanmaz çelikler genellikle yüzde 12 ile yüzde 18 arasında krom ve az miktarda nikel içerir. Çeliğin özellikleri yalnızca bileşimine değil, uygulanan ısıl işleme de bağlıdır.
Çelik, erimiş dökme demirdeki karbon oranını istenen düzeye düşürerek ve içindeki öbür katışkıları gidererek elde edilir. Bu nedenle çelik üretimi temel olarak bir arıtma işlemidir. Çağdaş sanayi toplumlarında milyonlarca tonluk hurda demir biriktiğinden, üstelik bu hurdaların eritilmesi kolay olduğundan, fabrika ve kullanım artığı hurda demirler çelik üretiminde hammadde olarak önemli bir yer tutar.
Bessemer İşlemi
Erimiş demirden sanayinin gereksinimini karşılayacak kadar büyük çapta çelik üretme yöntemini ilk kez 1856’da İngiliz mucit Henry Bessemer buldu. Bessemer işleminin temeli, erimiş demirin içine yaklaşık 20 dakika süreyle hava üflemeye dayanır. Bu işlemde kullanılan Bessemer dönüştürücüsü ya da konvertörü yüksek fırın gibi dik duran, ama yataklanmış millerin üzerine oturtulduğu için erimiş demiri doldurmak, hava üflemek ve çeliği boşaltmak gerektiğinde eğilebilen, kabaca armut biçiminde bir kaptır.
Kabın dibindeki bir dizi memeden ya da hava deliğinden erimiş demirin içine hava gönderilir. Böylece demir alaşımındaki karbon ve öbür katışkılar havanın oksijeniyle birleşerek “yükseltgenir” ya da yanar, daha doğrusu oksit haline gelir. Bu gaz halindeki oksitler parlak bir alevle yanarak hızla dönüştürücünün tepesine doğru yükselir ve ağzından dışarı çıkar. Yaklaşık 20 dakika sonra bütün yabancı maddeler oksit halinde uçup geriye katışıksız demir kalınca alevin biçimi ve rengi birden değişir. Bunun üzerine dönüştürücünün başındaki teknisyen üflenen havayı keser. Dönüştürücüdeki çelik bir potaya dökülürken aynı anda karbon ve öbür alaşım elementleri de potaya katılarak çeliğin yapısı istenildiği gibi ayarlanabilir.
Bazik Oksijen Yöntemi
Bessemer dönüştürücülerinin başlıca sakıncası, içeri üflenen havadaki azotun varlığından kaynaklanan büyük enerji kaybıdır. Dökme demirdeki karbon ve öbür elementlerin yanmasıyla açığa çıkan ısının büyük bölümünü azot soğurduğu için, çeliğin erime sıcaklığına ulaşmak çok uzun sürüyordu. Düşük maliyetle havadan bol miktarda oksijen elde etme yönteminin bulunması azotun ve Bessemer işleminin bu sakıncasını gidererek çelik üretiminde bir devrim yarattı. Bu yeni yöntemde, erimiş demir banyosunun üzerine suyla soğutulan borulardan büyük bir basınç altında arı oksijen püskürtülür.
Oksijenle çelik üretiminde LD, Kaldo ve Rotor adıyla bilinen üç temel yöntem uygulanır. İlk kez Avusturya’daki Linz ve Donawitz kentlerinde uygulandığı için bu kentlerin ilk harfleriyle anılan LD yönteminde, erimiş demir banyosunun yüzeyine yüksek basınçla oksijen püskürtülür. Bu yöntem çok hızlı bir arıtma sağlar ve yükleme kapasitesi 350 ton olan modern bir fırında yüzde 70’i dökme demir, yüzde 30’u hurda demirden oluşan eriyik 40 dakikada çeliğe dönüşür. Yüksek oranda fosfor içeren dökme demirleri LD yöntemiyle arıtmak için fırına oksijenle birlikte kireç de püskürtülür. Kirecin işlevi eriyikteki fosfor oksitleri soğuran bazik bir cüruf oluşturmaktır. Bu cüruf aynı zamanda değerli bir fosfat gübresidir. Bugün dünya çelik üretiminin yüzde 60’tan fazlası LD ya da bazik oksijen yöntemiyle gerçekleştirilmektedir.
Kaldo ve Rotor yöntemleri de LD yöntemiyle aynı temel ilkeye dayanır; aralarındaki tek fark bunlarda dönüştürücünün işlem sırasında yavaşça dönmesidir.
Siemens-Martin Fırını
Siemens-Martin fırınlarıyla çelik üretme yöntemi neredeyse bir yüzyıl boyunca bütün çelik üretiminin temeli olarak önemini korudu; ama bugün bu fırınların yerini büyük ölçüde bazik oksijen dönüştürücüleri ve elektrik arkı fırınları almıştır. Siemens-Martin fırını ya da öbür adıyla yansımalı fırın, duvarları ve tavanı ateşe dayanıklı tuğlalarla örülmüş uzun, yassı ve sığ bir fırındır. Gazla ısıtılan fırının her iki ucunda tuğla örgüyle ayrılmış birer odacık bulunur. Bu odacıkların birinden hava üflenir; yanma sırasında fırının içinde oluşan sıcak gazlar öbür odacıktan geçerek orayı ısıttıktan sonra yüksek bir bacayla dışarı atılır. Yaklaşık her 20 dakikada bir fırındaki bu hava ve sıcak gaz akımının yönü tersine çevrilir. Böylece yakıt ve hava önce bir odacıktan verilip sıcak fırın gazları öbür odacıktan çıkarken, 20 dakika sonra akım tersine çevrilince fırına verilen hava biraz önce sıcak gazların geçerek ısıttığı odacıktan geçer. Sonuçta, fırına üflenen havaya bir ön ısıtma uygulanmış olur; bu da fırının içindeki sıcaklığı artırır.
Siemens-Martin fırınına önce hurda demirçelik ve kireçtaşı yüklenir. Bu karışım biraz eriyince bu kez erimiş demir katılır. Arıtma için gerekli oksijen de ya fırına demir oksit yükleyerek ya da suyla soğutulan bir borudan doğrudan oksijen püskürterek sağlanır.
İstenen karbon oranına ulaşıldığında çelik ve üstünde yüzen cüruf önce aynı potaya akıtılır; sonra cüruf bu potanın üstünden taşırılarak yandaki daha küçük bir potaya alınır. Alaşımda bulunması istenen öbür maddeler de çelik akıtılırken potaya eklenir. SiemensMartin yöntemiyle elde edilen çelik üstün niteliklidir ama işlem oldukça yavaştır; 350 ton kapasiteli bir Siemens-Martin fırınında çeliğin erime süresi yaklaşık 10 saati bulur.
Elektrik Arkı Fırını
Üstün nitelikli özel alaşım çelikleri genellikle elektrik arkı fırınlarında üretilir. Yükleme kapasitesi ortalama 150 ton olan bu fırınların gövdesi yuvarlaktır, derinliği fazla değildir ve içi ateşe dayanıklı tuğlayla astarlanmıştır. Fırının kubbe biçimindeki tavanı açılabildiği için soğuk hurda demir buradan yüklenir. Fırını ısıtmak için gerekli ısı da tavandan aşağı doğru uzanan üç karbon elektrotun ürettiği elektrik arkıyla sağlanır. Elektrotların alt uçları çeliğe değmez; ama elektrik akımının bu uçlardan çeliğe atlamasıyla oluşan elektrik arkının yoğun ısısı hurda çeliği kısa sürede eritir. Çeliğin içindeki katışkılar da öbür yöntemlerdeki gibi giderilir. Çeliğin bileşimini belirlemek üzere örnek alındıktan ve yüzeyde toplanan cüruf akıtıldıktan sonra fırın eğilerek içindeki erimiş çelik potaya dökülür.
En üstün nitelikli çelikler elektrik arkı fırınlarıyla üretilir; çünkü bu fırınların ısı kaynağı kazanda gelişen kimyasal tepkimelerden bağımsızdır ve kolayca denetlenebilir. Bu nedenle alaşımda bulunması istenen elementler sonradan potaya koymak yerine doğrudan fırındaki eriyiğe katılabilir. Elektrik arkı fırınları bu üstünlüğüyle paslanmaz çeliklerin ve hemen hemen bütün üstün nitelikli özel alaşım çeliklerinin üretiminde öbür yöntemlerin yerini almıştır.
İstenmeyen bütün katışkılardan temizlenmiş, son derece arı çelik üretmek gerektiğinde, eriyen çelik özel bir potaya alınır ve vakumlu bir odaya götürülerek içinde çözünmüş durumda bulunan bütün gazların çıkması sağlanır. Örneğin motor yataklarının yapımında kullanılan özel çelikler bu yöntemle üretilir.
Çelik üretiminde kullanılan başka tip bir elektrik fırını da indükleme fırınıdır. Daha çok özel takım çeliklerinin üretildiği bu fırınlar ayrıca çelik dökümhanelerinde küçük eritme birimi olarak da kullanılır. Büyüklüğü ve biçimiyle bir çöp bidonuna benzeyen bu fırının çevresine sarılmış olan bakır bobinden güçlü bir elektrik akımı geçirilir. Fırına yüklemeden önce ayıklanarak katışıksız olmasına özen gösterilen hurda çelik ve öbür hammaddeler indüklemeyle ısıtılır, eritilir ve karıştırılır. Gaz türbinlerinin yapımında kullanılan nikel-krom-kobaltlı alaşımları ve yüksek sıcaklıklara dayanıklı özel çelikleri üretm ek için kurulan indükleme fırınları genellikle vakumlu odalarda çalıştırılır.
Çeliğe Biçim Verme
Fırından potaya akıtılan erimiş çelik bir sonraki aşama olan döküme hazır demektir. Üretilen çeliğin bir bölümü, dökme çelik parçalar yapmak üzere istenen biçimlerde hazırlanmış olan kum kalıplara akıtılır. Geri kalanı da dökme demirden yapılmış kalın çeperli, büyük kalıplara dökülür ve sonradan çekiçle dövülerek, preslenerek ya da haddelenerek biçimlendirilecek olan çelik külçelere dönüştürülür. Kütük ya da ingot olarak da bilinen bu çelik külçelerin ağırlığı birkaç yüz kilogramdan birkaç yüz tona kadar değişir. Hadde tezgâhında işlenecek olan külçeler genellikle 30 tonun altında; ince çubuk, tel ve ensiz şerit üretiminde kullanılacak külçelerin ağırlığı yaklaşık 6 ton; geniş ya da kalın çelik levha üretiminde kullamlanlarınki ise genellikle 25 ton kadardır.
Haddelemeye elverişli küçük ve yassı külçelerin üretiminde daha çok sürekli döküm yöntemi uygulanır. Bu yöntemde, erimiş çelik suyla soğutulan üstü ve altı açık bakır kalıplara dökülür. Böylece kalıbın içinde katılaştıkça alttan sürekli çekilerek alman çelik külçeler doğrudan hadde tezgâhına gönderilebilir.
Toplam çelik üretiminin yüzde 90’dan daha büyük bölümü sıcak külçelerin haddelenmesiyle biçimlendirilir. Bu işlemin temeli, kalın çelik külçeleri “hadde” denen merdanelerin arasından geçirerek yassıltıp levha haline getirmektir. Tıpkı çamaşır makinelerinin sıkma merdaneleri gibi düzenlenmiş olan bu haddeler eşit hızla, ama birbirine ters yönde döner. Hadde tezgâhlarında genellikle çok sayıda hadde grubu vardır ve her gruptan geçişte çelik levha biraz daha incelir. Çeliğin düzgün ve pürüzsüz yüzeyli haddelerden geçirilmesiyle levha, yaprak ve sac gibi ürünler elde edilebilir; yalnız teneke kutuların yapımında kullanılan ince çelik sacların yüzeyine sonradan elektroliz yöntemiyle çok ince ve katışıksız bir kalay katmanı kaplanır. Haddelerin yüzeyine yiv ve setler açıldığında demiryolu rayları, çelik yapı kirişleri, yuvarlak, kare ve altıgen kesitli yapı çubukları gibi değişik biçim ve kalınlıkta haddelenmiş ürünler elde edilir. Aralarındaki sivri uçlu bir mille belirli bir açı yapacak biçimde yerleştirilmiş olan konik haddelerle de dikişsiz çelik borular üretilebilir.
Sıcak çeliği biçimlendirmek kolaydır; üstelik sıcak işleme çeliğin niteliğini de artırır. Bu yüzden sıcak haddelenmiş ya da dövülmüş çeliğin kopma direnci dökme çeliğe oranla daha fazladır. Sıcak haddelemenin tek sakıncası, hadde gruplarının arasından geçirilen çeliğin inceldikçe daha çabuk soğuması ve yeniden ısıtmak hem zaman, hem ek enerji gerektirdiğinden maliyetin yükselmesidir. Bu nedenle ince kesitli çelik ürünler genellikle soğukken işlenir. Örneğin çelik metre şeritleri soğuk haddelemeyle, çelik teller ise soğuk çelik çubukların ince kalıplardan çekilmesiyle yapılır. Çelik borular da genellikle soğuk çekmeyle üretilir. Çelik ürünlere soğuk işlemede istenen boyutu vermek sıcak işlemeden daha kolay, üstelik bu ürünlerin yüzeyi daha düzgün ve parlaktır.
Isıl İşlemler
Çelik ısıya karşı son derece duyarlıdır. Akkor hale gelinceye kadar ısıtılıp, sonra çok yavaş olarak soğutulduğunda yumuşar. Buna çeliğin tavlanması denir. Dökümden ya da dövmeden sonra çeliğin iç gerilimlerini gidermek üzere, işlenmiş parçalar önce ısıtılıp sonra havayla soğutularak normalleştirilebilir. Bu ısıl işlemlerin her ikisi de çeliğin kopma direncini artırdığı için ürünün kopmaksızın bükülmesini ya da gerilmesini sağlar. Bu nedenle çeliğin kopma direncini ve dövülebilirlik özelliğini artırmak için soğuk işleme sırasında ya da sonrasında tavlama ve normalleştirme işlemleri uygulanabilir.
800°-900°C’ye kadar ısıtılarak akkor haline gelmiş çelik kızgın haldeyken suya, tuzlu suya ya da yağa daldırılarak hızla soğutulursa sertleşir; bu işleme su verme denir. Su verme işleminde çeliğin soğuma hızı işlenen çeliğin türüne ve elde edilmek istenen sertliğe bağlıdır. Çok soğuk tuzlu suda çeliğin soğuma hızı en yüksek, yağda biraz daha yavaş, kızgın yağda ya da erimiş kurşun banyosunda en düşüktür. Bazı yüksek alaşımlı çelikler havayla soğutularak sertleştirilir.
Su verme işleminden sonra çeliklerin çoğu kullanılamayacak kadar gevrekleşir. Bu nedenle, sertlik derecesi ile çekme ve kopma direncinin en iyi bileşimini elde etmek için, su verme işleminden sonra çelik daha düşük bir sıcaklığa (250°-650°C) kadar yeniden ısıtılır ve yavaş yavaş soğutulur. Bu ısıl işleme de temperleme denir.
Tarih
Kalde’deki Ur kenti gibi birçok arkeolojik yerleşmede ve Mısır piramitlerinde demirden yapılma eşyalar bulunmuştur. Arkeolojik kazılardaki buluntulardan anlaşıldığı kadarıyla, kullanılan ilk demir meteorit kökenliydi ve yalnızca silah, mücevher gibi eşyaların yapımında kullanılacak kadar değerli bir gereçti. Demir cevherlerini eriterek büyük miktarda demir elde etmenin yolu ancak İÖ 1500 yıllarında bulundu.
Demir ile çelik arasındaki fark 19. yüzyılın başlarına kadar yeterince anlaşılamamıştı. O yüzyıla kadar demiri eritmek için, üstüne kısa bir baca dikilmiş, basit ocaklar kullanılıyordu. Bu ocak hava deliği düzeyine kadar odunkömürüyle doldurulur, onun üstüne demir cevheri ile odunkömürü karışımı yığılır ve odunkömürü ateşlendikten sonra ocağa körükle hava basılırdı. Hemen hemen katışıksız karbon olan odunkömürü, cevherdeki demir oksidin oksijeniyle birleşip karbon monoksit gazı halinde bacadan çıkarken, ocağın tabanında macun kıvamında sıcak bir demir ve cüruf topağı kalırdı. Bu topak ocaktan alınır, çekiçle dövülerek hem biçimlendirilir, hem de içindeki cürufun demirden ayrılması sağlanırdı. Soğudukça yeniden ısıtılır ve iyice incelerek çubuk haline gelinceye kadar dövme işlemi sürdürülürdü. Bu yöntemle elde edilen demir oldukça katışkılıydı, ama gene de alet yapımı için değerli bir hammaddeydi. Yalnız, genellikle yumuşak olan bu demirden istenen nitelikte silah yapılamıyordu. Bu üretime çok daha elverişli olan çelik bir rastlantı sonucunda bulundu. Demirciler farkında olmaksızın karbon oranı her zamankinden daha yüksek olan bir demir banyosu hazırladıklarında bu demirin “çelikleştiğini” gördüler. Bu yeni ürün su verildiğinde, yani kızgın haldeyken suya batırıldığında sertleşiyor, sıcakken yavaş yavaş soğutularak temperlendiğinde çekme ve kopma direjıci artıyordu. Dövülmüş demir çubukları odunkömürü ocaklarında ısıtarak, sınama yanılma yoluyla çeşitli ısıl işlem yöntemleri geliştirdiler. İspanya, Şam ve Japonya’daki kılıç yapımcıları, tunçtan ya da demirden yapılmış silah ve zırhları delebilecek kadar keskin ve sağlam kılıçlar yapabilmek için az ve çok karbonlu çelik çubukları bir arada dövmeyi öğrenmişlerdi.
18. yüzyılın başında İngiliz demir ustası Abraham Darby ve oğlu bugünkü yüksek fırınların öncüsü olan bir fırın yaptılar. Karbon kaynağı ve yakıt olarak kokkömürü kullanıyor, fırına daha yüksek bir hava akımı sağlayabilmek için buhar makinelerinden yararlanıyorlardı. Kokkömürü iyi bir karbon kaynağıydı; çünkü içindeki yabancı maddeler koklaştırma sırasında gaz haline geçerek zaten uçup gitmiş oluyordu. Üstelik, içinden şiddetli bir hava akımının geçebileceği gözenekli bir yığın oluşturduğundan, fırındaki demir cevheri ile kireçtaşı için iyi bir destekti. Zamanla fırın sıcaklığı artırılarak demirin daha kısa sürede erimesi sağlandı. Başlangıçta kokkömüründen elde edilen demirin dünya üretimindeki payı çok azdı. Ama 19. yüzyılda 100 milyon tonun üstüne çıktı ve bu yöntemle üretilen dökme demir birçok alanda dövme demirin, ahşabın, bakır ve pirincin yerini aldı. 19. yüzyılın başlarında odunkömürüyle demir üreten pek az fırın kalmış ve demir-çelik sanayisi kömür ocaklarına yakın alanlarda toplanmıştı.
1740’larda Benjamin Huntsman çeliği eriterek büyük külçeler halinde kalıplamanın yolunu buldu. Özel bir kil karışımını kalıplayarak, çeliğin erime sıcaklığına dayanabilecek güçte bir pota yapıyor ve bu potayı bir odunkömürü ocağına oturtarak çelik çubukları bunun içinde eritiyordu. Daha sonra ocaktan alman potanın içindeki sıvı çelik, dökme demirden yapılmış kalıplara dökülerek külçe haline getiriliyordu. Çeliği eriterek içindeki yapısal kararsızlıkları gideren bu yöntem büyük bir ilerlemeydi. Huntsman yöntemini yıllarca gizli tuttu; ama sonunda öğrenilerek İngiltere’deki bıçak ve takım çeliği yapımcıları arasında hızla yayıldı.
1784’te Henry Cort dökme demirin kırılganlığını azaltarak dövülmeye elverişli duruma getirmek için pudlaj yöntemini tasarladı. Bu yöntemde, fırındaki erimiş demir banyosu çubuklarla karıştırılıyor ve hava ile cürufun eriyik içinde iyice dağılması sağlanıyordu. Böylece havayla tepkimeye giren karbon gaz halinde fırından çıkarken, silisyum, manganez ve fosfor gibi katışkılar da oksitlenerek demirden ayrılıyordu. Ocakta kalan macun kıvamındaki demir ise su gücüyle çalışan şahmerdanla dövülerek biçimlendiriliyordu. Bu pudlaj demiri hemen hemen katışıksız, dökme demirden daha yumuşak ve daha az gevrekti. Bu nedenle köprü, gemi, makine yapımında ve gene Cort’un geliştirdiği bir haddeleme yöntemiyle demiryolu raylarının üretiminde kullanılıyordu.
Bessemer’in 1856’da geliştirdiği dönüştürücü, çeliğin ilk kez sanayi çapında üretilmesini sağladı. Ertesi yıl İngiltere’de William ve Friedrich Siemens kardeşlerin bulduğu, bir süre sonra Fransa’da Pierre Martin’in geliştirdiği Siemens-Martin fırını ise çelik sanayisinde ikinci büyük adım oldu. Özellikle Bessemer dönüştürücüsünde yeterince antılamayan, fosfor oranı yüksek demir cevherlerinin işlenmesinde bu fırın çok iyi sonuç veriyordu. Fosfor oranı yüksek cevherleri değerlendirmenin başka bir yöntemini 1877’de Percy Gilchrist ile Sidney G. Thomas buldular. Bu iki İngiliz mühendis Bessemer dönüştürücüsünün içini dolomitle astarlamış ve erimiş çeliğe kireçtaşı katarak fosforu ayırmayı başarmıştı.
Dünyanın en büyük dökme demir ve hamçelik üreticileri SSCB, Japonya ve ABD’dir. Türkiye’de demir-çelik üretiminin büyük bölümünü gerçekleştiren Ereğli, İskenderun, Karabük ve Kınkkale fabrikalannda SiemensM artin fırınları kullanılır. Özel çelik fabrikaları ise genellikle elektrik arkı fırınlarıyla, bir bölümü de Bessemer işlemiyle çelik üretir.
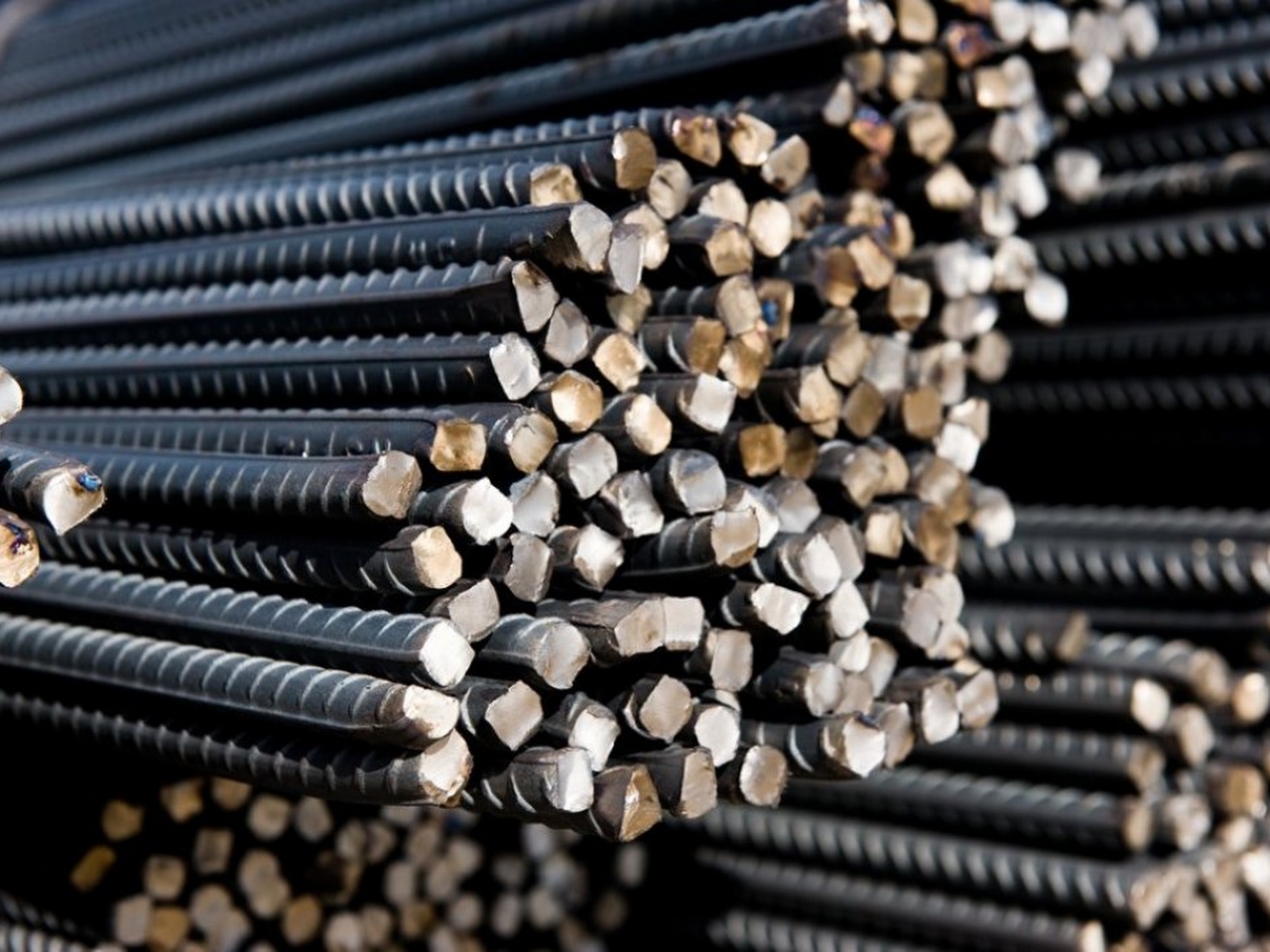