Kaynak (Yöntem)
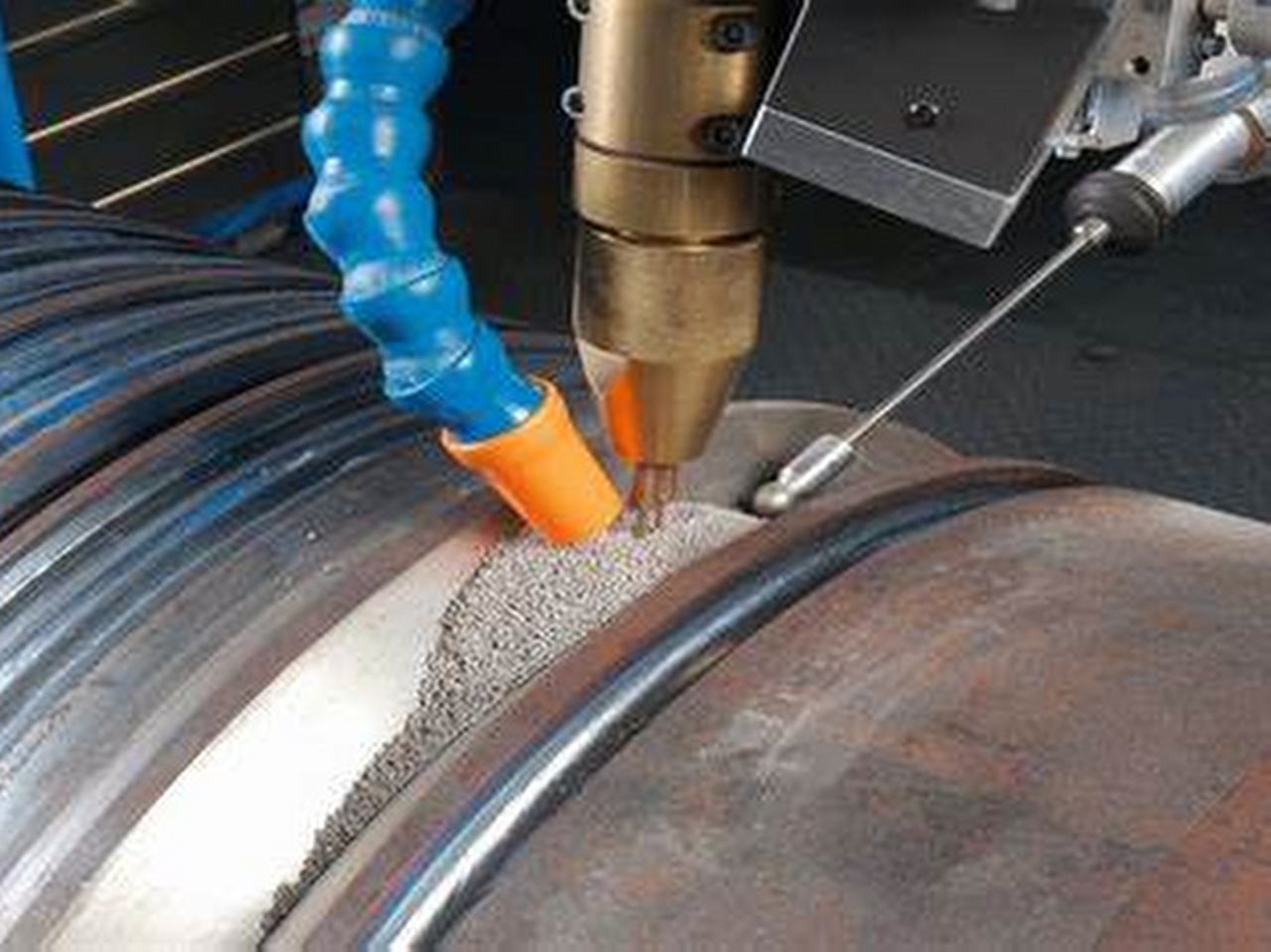
Kaynak, benzer iki metali, cıvata ya da perçin gibi herhangi bir ek bağlama öğesi kullanmadan birleştirme yöntemine denir. Eskiden demirciler, metal parçalarını sıcak haldeyken çekiçle döverek birleştirirlerdi. Bu yöntemde, iki metal parçası erime noktasına yaklaşıncaya kadar ısıtılır, metallerin yüzeyindeki yanmış kabuk hızla temizlenir ve iki parça, üst üste konarak çekiçle dövülürdü. Yumuşak ve plastik hale gelen metal parçaları sıkışarak kaynaşırdı.
Metaller, genellikle dövülerek ya da eritilerek kaynaklanır. Eritmeli kaynakta, metal parçalarının temas noktaları, eriyip birikirleriyle kaynaşana kadar ısıtılır. Bu işlemde ısı, elektrik arkından, gaz alevinden ya da termit denen kızgın bir eritme metalinden elde edilir. Döverek kaynaklamada da aynı ısı kaynaklarından yararlanılabilir; ama bunlara ek olarak demirci ocaklarındaki açık ateş de kullanılabilir.
Eritmeli Kaynak
En yaygın uygulanan eritmeli kaynak yöntemi elektrik arkı kaynağıdır. Eğer güçlü bir elektrik akımı devresinde, kısa bir boşluk varsa, bu aralıkta elektrik arkı oluşur. Milyonlarca yüklü parçacık bu boşluğu havadan atlayarak geçmeye çalışır; işte bu milyonlarca parçacığın güçlü ışık saçarak havada oluşturdukları kıvılcım demetine elektrik arkı denir. Bu ark olağanüstü derecede sıcaktır ve sıcaklığı 3.500°C’ye ulaşır. “Hamlaç” denen ayarlı bir musluktan püskürtülen gaz alevi OKSİJEN maddesinde anlatılmıştır. Termit metali ise alüminyum ve demir oksit karışımından oluşan yanıcı bir tozdur. Termit yakıldığında 2.500°C civarında bir sıcaklık elde edilir; bu sıcaklıkta çelik kolayca erir.
Bir elektrik arkı kaynağında ark, iki karbon çubuk arasında va da kaynak yapılacak metal ile bir karbon ya da metal çubuk arasında oluşturulur. Bu metal ya da karbon çubuklara kaynak elektrotu denir. Metal elektrot kullanılırken, arkın oluşturduğu ısı elektrotu eritir ve eriyen metal, kaynak yapılan noktaya dolar. Karbon elektrot kullanıldığı zaman ise, ayrıca metal bir dolgu çubuğunun kullanılması gerekir. Bu dolgu çubuğu eriyerek kaynak noktasının sıvı metalle dolmasını sağlar.
Eritmeli kaynak sırasında, kaynaklanacak metalin niteliğine bağlı olarak, eritici denen özel bir madde kullanılır. Eritici, kaynak noktasında yanmış bir kabuk katmanının oluşmasını önler ve böylece metalin akmasını kolaylaştırır. Elektrik arkı kaynağında dolgu çubuğunun üzerinde bir eritici katmanı bulunur.
Gaz kaynağında oksijen ve asetilen gazları birlikte yakılarak 3.000°C sıcaklığında bir alev elde edilir. Burada da, kaynak noktasına sıvı metal doldurmak için bir dolgu çubuğundan yararlanılır. Dolgu çubuğu genellikle bakırla kaplanmıştır; eritici ise bir macun ya da toz biçiminde ayrıca uygulanır. Çubuğun ucu kaynaktan önce ve kaynak sırasında, arada bir eriticiye batırılır.
Termit metaliyle kaynak yapmak için, kaynaklanacak demir ya da çelik parçaları, bir kum kalıbına yerleştirilir ve birleştirilecek yüzeyin çevresi kumla sıkıştırılır. Sonra, parçalar arasındaki aralığa parçaların yüzeyi eriyinceye kadar erimiş termit metali dökülür. Soğuma sırasında, çelik parçaları ile termit metali birbiriyle kaynaşır.
Sıcak Dövme Kaynağı
Döverek kaynaklamada, kaynaklanacak metali ısıtmak için elektrikten yararlanılabilir. Kaynaklanacak metal parçalarına elektrik akımı verildiğinde parçaların sıcaklığı, metalin erime noktasına kadar artar. (Bütün elektrik iletkenleri, içlerinden akım geçtiğinde ısınır; bu ısınmanın derecesi, elektrik akımının şiddetine bağlıdır.) Metallerin elektrik akımına en büyük direnç gösterdikleri yer, birbirlerine temas ettikleri kaynak bölgesidir, bu nedenle de en fazla bu nokta ısınır.
Elektrik akımı, kaynak noktası iyice yumuşayana kadar metallerden geçirilir. Sonra akım kesilir, basınç uygulanarak iki metal birbirine bastırılır ve böylece kaynaşmaları sağlanır.
İnce metal levhalarının (sac), “nokta kaynağı” denen yöntemle kaynaklanmasında, yukarıda anlatılan sıcak dövme kaynağı tekniğinden yararlanılır. Bu işlemde iki metal levha, kenarları üst üste binecek biçimde birleştirilir ve elektrik kaynağına bağlı iki bakır elektrot arasında sıkıştırılırlar. Elektrotlar arasından geçirilen güçlü bir elektrik akımı, metal levhaların temas noktasında kaynaşmalarını sağlar. Nokta kaynağı çok kısa bir süre içinde tamamlanır ve elektrotlar derhal bir başka noktaya kaydırılabilir.
Sıcak termit metali kullanılarak yapılan dövme kaynağı sırasında, birleştirilecek demir ya da çelik parçaları bir kum kalıbı içine yerleştirilir. Kaynak noktasına kızgın termit metali dökülür ve parçalar iyice yumuşayınca basınçla sıkıştırılarak birbirine kaynaklanır. Kaynak soğuduktan sonra, artık termit metali temizlenir.
Normal çelikler, buraya kadar anlatılan yöntemlerden herhangi biriyle kaynaklanabilir. Özel çelik alaşımlarını ya da bakır ve alüminyum gibi metalleri kaynaklamak için ise, bunlardan biraz daha değişik yöntemlerin uygulanması gerekir.
Uzun zaman alüminyumun kaynaklanmasında güçlük çekildi, çünkü alüminyum ısındığında derhal havadaki oksijenle birleşir, yani yükseltgenir. Bu durum kaynağın zayıflamasına yol açar. Günümüzde, bu tür metallere kaynak yapılırken, metalin yüzeyine eylemsiz, yani tepkimeye girmeyen gazlar, özellikle de argon gazı püskürtülür. Bu gaz örtüsü, eriyen alüminyumun havayla temasını engeller, böylece metalin yükseltgenmesi engellenir. Bu tür gaz örtülü kaynak teknikleri, özellikle uçak yapımı sırasında uygulanır.
Çok çeşitli ürünün yapımı sırasında kaynak işlemine başvurulur. Günümüzde pek çok yeni kaynak tekniği geliştirilmiştir. Bu yöntemlerin birinde, hidrojen atomlarından oluşan çok sıcak bir alev püskürüğünden yararlanılır. Alaşım çeliklerini kaynaklayabilmek için bundan daha yüksek bir ısıya gerek duyulur; bu sıcaklığı elde etmenin bir yolu, kaynak yapılacak metale elektron tabancasıyla üretilen bir elektron demeti yollamak olabilir. Lazerler de kaynak yapmakta kullanılabilir; bilgisayar denetimiyle, kaynak noktasında odaklanmış ısı elde edilebilir.
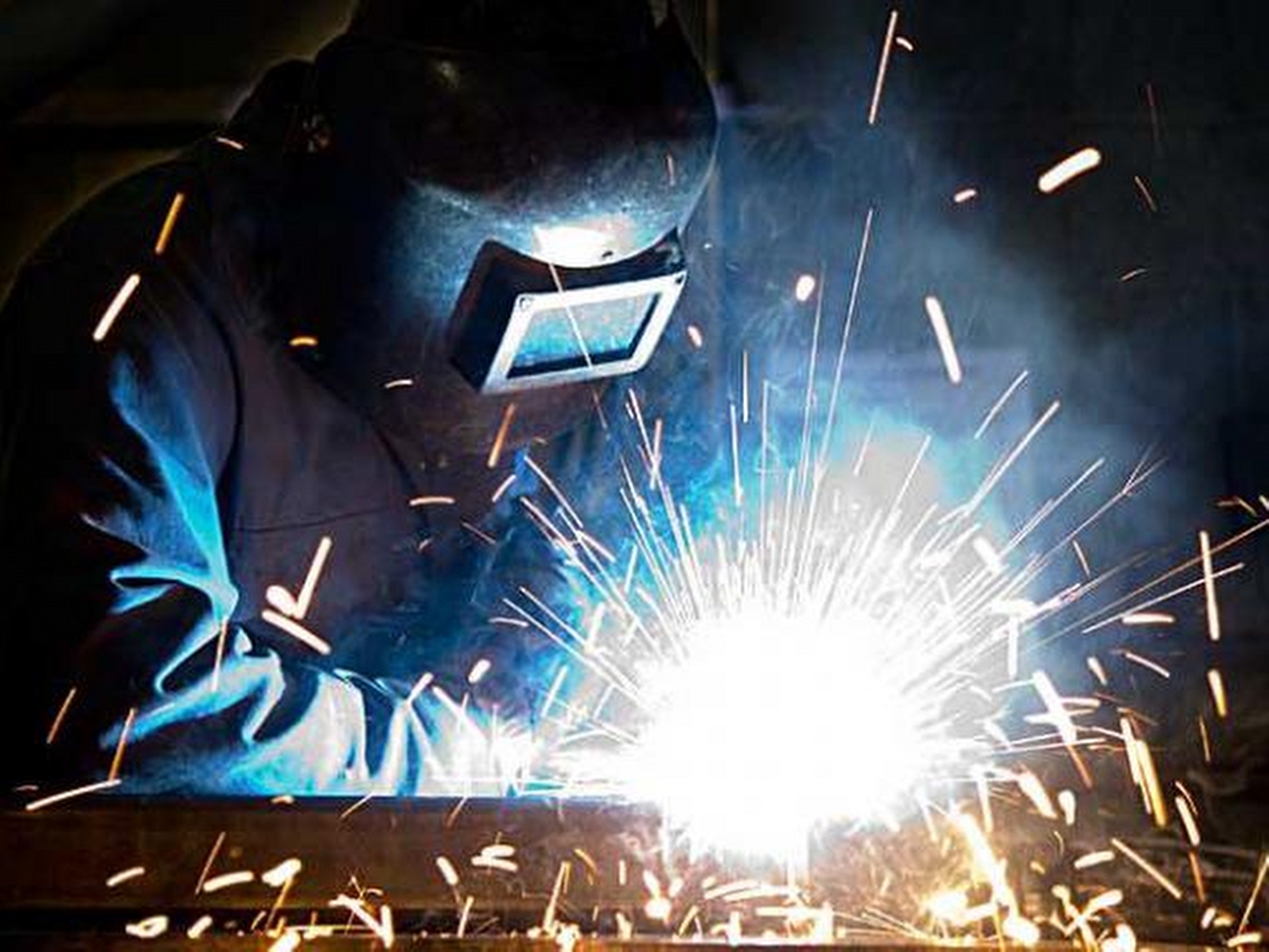